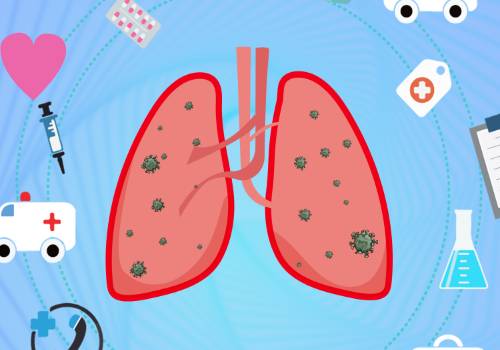
内容涉及:处方;西林瓶;胶塞;预冻;一次干燥;二次干燥;冻干显微镜
弗戈工业在线 2023-08-01 17:44:17
内容涉及:
处方;
西林瓶;
(资料图)
胶塞;
预冻;
一次干燥;
二次干燥;
冻干显微镜;
DSC;
其他; 这些内容准备分五篇文章发出来; 一些需要系统回答的问题,不包含在此集锦中; 需要系统回答的问题,因为要写清楚前因、后果、以及各种可能性。整个回答会比较庞大;后期针对这种问题也许会整理成单独的文章,一篇篇发出来;
处 方
1、蛋白质API产品,对于不同产品的不同规格,只改变蛋白浓度,辅料的组成和含量不变,冻干工艺需要调整吗?如果需要,如何调整?
答:蛋白浓度的提高,会增加升华的阻力同时通常也会提高产品的塌陷温度;
前者让升华变“难”,后者可以使得样品承受“产品温度”更高的冻干工艺;
但通常来说,蛋白浓度的增加会使得冻干更加容易;
如:蛋白浓度从10%提高到60%,会大幅提高产品塌陷温度,冻干时间可以大幅缩短;
*纯蛋白溶液的Tg‘大概是-10℃;注意这里是大幅提高塌陷温度Tc,对玻璃态转变温度Tg’的改变可能没有那么明显;
了解详情可以参考之前的文章:冻干蛋白制剂处方设计:一些实用性建议
2、如果不是蛋白产品,API的量增加,也会让冻干更加容易么?
答:这个肯定不是的,具体问题具体分析。要看API对于样品整体关键温度的影响是提高还是降低,另外产品的阻力也需要通过实验确认,不能一概而论。
如果不能提高塌陷温度的话,通常提高溶质浓度,是使得冻干更难;
3、样品中的成分,只有API和甘露醇,复溶后出现样品浑浊的现象。是因为使用了甘露醇导致浑浊吗?
答:用甘露醇作辅料的蛋白产品非常多,也并没有出现最终产品浑浊的现象。
可能引起澄清度不达标的原因:
甘露醇原料中存在杂质;
蛋白产品,甘露醇作为蛋白质稳定剂,在冷冻过程中先于蛋白质结晶,使得蛋白质失去保护从而变性;
甘露醇的比表面积较大,很容易吸附如:胶塞中脱落的、包材和处理过程中的其他杂质,在复溶过程中表现为浑浊;
冻干机漏硅油,也是导致浑浊的原因之一。建 议:
可以对单独的甘露醇辅料进行冻干,看是否有浑浊的现象,以排除甘露醇原料中存在杂质的可能。
更换一台冻干机运行同样的工艺,考察结果;
正常甘露醇样品冻干非常容易,复溶快速且澄清透明;
对复溶后样品进行过滤,取滤膜上截留的物质进行分析,反追溯不溶性微粒的来源。
3、使用乳糖作为赋形剂如何?查到一些冻干产品使用的是乳糖作为赋形剂。
答:乳糖作为赋性剂不是一个好的选择;乳糖会和蛋白质的功能基团以及其他化学分子发生化学反应;
曾经用乳糖作为人生长激素的赋形剂,在室温25℃放置一个月之后,约50%的蛋白质都发生了降解。降解的原因不是因为蛋白聚集,而是化学降解;
而且乳糖的塌陷温度为-31℃,加入乳糖会导致体系的关键温度降低;
如果原研药使用了乳糖,那仿制药必须也要使用相同的赋形剂;
但是如果是新药,建议不要选择乳糖。
5、处方中含有赋形剂、盐,冻干需要注意什么?
答:赋性剂如果使用甘露醇、甘氨酸作为赋形剂,他们的共晶点温度都比较高,可以在较高的温度下进行冻干,时间也比较短;
但这些晶体物质的不完全结晶是个问题,需要在预冻阶段进行研究;
冻干配方中,尽量避免使用盐。添加了盐会使得体系的关键温度大幅降低,如果一定要使用,最好控制在3%以下,最高不能超过5%;
6、如果一个制剂有两种处方可以选,是否一定选择Tg较高的处方?
答:不一定。
Tg只是处方筛选过程中考察的指标之一,而且常常不是最重要的指标;
对于冻干产品来说,Tg只要高于正常存储温度就可以了。海藻糖Tg大约120℃、蔗糖Tg 70℃多,都高于存储温度,区别并不大;
冻干是为了解决样品稳定性的问题,所以稳定性是处方选择是要考虑的第一目标;
然后是效率(比如选择Tc更高的处方);
再然后可能才是考虑Tg,或者还要更靠后一些,不是一个排名非常靠前的考虑因素。还是你问的是Tg’?那影响更大一些。
Tg是冻干后干物质的玻璃态转变温度,Tg’是浓缩溶液的玻璃态转变温度,这是两个参数;
7、虽说不建议处方中添加盐类物质,但如果处方中已经确定含有NACL了,另外还有蔗糖做保护剂。对于这种处方的冻干工艺开发,有什么具体的建议?
答:如果处方中已经确定需要添加NACL,则注意添加比例不要太高;
添加了NACL的处方,冻干前一定要测关键温度,因为体系的关键温度可能低于这个处方中你添加的的任何一项辅料的关键温度,这通常是无法预估的;
同时建议测一个退火后的塌陷温度测试,这类处方通过退火提高塌陷温度的几率较大,值得尝试;
8、冻干产品属于晶型还是非晶型是本身的处方决定的,还是冻干工艺决定的?
答:这两个因素都有可能影响。
比如,辅料中含有甘露醇。如果预冻速度很快,甘露醇没有完成结晶而形成了无定形态的甘露醇,那最终的产品可能就是非晶型或者混合晶型;
如果预冻降温速率比较慢,或者在预冻工艺中加入了退火,使得甘露醇得到彻底结晶,则最终产品可能就是晶型的;
不同晶型制剂的热力学稳定性不一样,可能导致降解速率不一致,介入可能影响产品的稳定性和生物利用度(但不是绝对的);
所以还是针对冻干后的产品考察CQA,以CQA考察的结果作为指导;
9、疫苗的冻干处方,如何选择氨基酸,比如组氨酸、精氨酸、赖氨酸?
答:氨基酸在整个冻干工艺过程中,需要保持无定形态;以使得其对疫苗发挥稳定作用;氨基酸物理化学状态,是选择氨基酸的一个重要标准;
具体实践中,可以对不同氨基酸处方的样品进行冷冻干燥,考察最终产品的稳定性以最终确认;
西林瓶
1、关于西林瓶的选择有那些建议?
答:这个问题问的比较宽泛,通常:
选择管制瓶更好,除非是大装量样品才会考虑模制瓶;
最好选择国际标准规格的瓶子,而不是非标西林瓶;
西林瓶的底更平,可以增加传热。但是太平的底对于自动进出料系统来说,在带子上传送不太容易。同时底太平也会容易碎瓶;
灌装容量通常不超过总容量的一半;
灌装高度最好不要超过2厘米,超过2厘米升华阻力大大增加,会导致工艺时间很长;
同样灌装高度,西林瓶容量越小则升华时间会越短(瓶壁传热面更大);
对于含有吐温的样品,选择西林瓶的时候需要通过实验测试一下是否会出现爬壁;接触的一些显示案例,发现西林瓶的碎瓶常常是因为西林瓶质量问题导致的,同样的样品,换一种瓶子问题就解决了;
2、选择管制瓶的话,那是底越平越好吗?
答:也不是越平越好。
如果你的工业冻干机配有自动进出料,底太平没有空隙,在传送带上传送比较困难;
另外底太平也可能导致碎瓶概率增大;
4、西林瓶碎瓶的原因有哪些?如何解决?
答:这个要看是实验室中试研究过程中发生的西林瓶破裂还是工业生产过程中出现的,原因会不大一样:
实验室研究阶段出现的破瓶:
西林瓶的质量问题(可能是材质问题),很多时候用户出现破瓶,换一个厂家的西林瓶,问题就解决了;
处方中含有甘露醇;
溶液装量过高,则破瓶概率增大;
预冻降温速度过快,有时也是诱因;
工业生产阶段出现的破瓶(这里特指在实验室研究阶段没有出现破瓶,却在工业生产阶段出现破瓶的现象):
上游工艺也可能导致西林瓶的破裂。清洗、灭菌过程中,玻璃上的划痕等都可能造成西林瓶易于破碎;西林瓶的质量问题:
西林瓶尺寸不够精准,外径偏大一点则西林瓶位于冻干托盘的框内,互相挤压产生的力就会很大(因此在托盘上放置小瓶时,也建议不要太紧摆放),从而导致西林瓶的破裂;
某些西林瓶的玻璃薄了一点,也可能导致西林瓶的破裂;
不均匀的过冷在工业生产阶段会比实验室更加严重,也会导致破瓶的比例增大;
5、西林瓶产品,灌装量一般是多少?
答:冻干产品灌装量一般不高于西林瓶总装量的½,但这只是为了冻干过程更经济以及复溶容易操作而提出的建议,并不是强制规定。
胶 塞
1、压塞时西林瓶内负压二次干燥结束后压塞,是在二次干燥的压力条件下,还是反填后压塞更合适?
答:从前企业大多在真空条件下直接压塞;
更好的方法是反填气体(很多时候是氮气)到0.7-0.9个大气压(根据产品装量),然后压塞;
这样有一定的负压,有大气压胶塞不容易跳塞;
负压不大,胶塞不易变形密封完整性也会更好;
在一定的负压条件下压塞,复溶时注入溶剂需要用的力更合理,拔针头的时候吸力也不会太大导致针头难拔;
对于最终样品含水量很低的样品维持水分数据也有一定好处;
2、冻干产品,放置期间水分升高是什么原因?
答:如果确定胶塞密封性没有问题的话,大概率就是胶塞水分迁移导致的;
3、胶塞水分
3.1如何判断产品水分升高是由胶塞水分迁移引起的?
答:由胶塞水分迁移带来的产品水分增加,在一定温度条件下,胶塞和产品的水分持续一段时间后会达到平衡;
你可以根据这个来设计实验,如果实验数据和这个匹配,那就是胶塞水分迁移带来的水分提高;
密封性问题导致的水分升高,会随着时间延长不断升高,不会有这个平衡(或者出现的很晚);
密封性问题导致水分升高在冻干产品里出现的很少,绝大部分都是胶塞导致的;
3.2你在课上说胶塞和产品的水分持续一段时间会达到平衡,这个时间大概时多久?除了时间还有其他影响因素么?
答:纠正一下,我说的完整的内容是:由胶塞水分迁移带来的产品水分增加(并不是任何原因导致的水分增加),在一定温度条件下,胶塞和产品的水分持续一段时间后会达到平衡;
第一相关条件是温度,温度越高达到平衡的时间就会越快;
这个时间可以是1周、2周、4周甚至更长时间,具体取决于当时的存储温度;
3.3那些产品对于胶塞水分需要特别注意,我们平时的产品没有很关注这个点,做产品也一直没有问题。
答:冻干前浓度低、总溶质含量少、最终产品对水分很敏感(目标水分低)的产品,易于被胶塞水分迁移的问题困扰。
每个用户的产品,都有自己特定的问题,你需要对产品和过程都很熟悉;
当然了,也有一些产品就是很容易,随便怎么做都可以做成。
但是做成不代表科学、高效,我会始终建议用户对自己的产品和整个冻干过程的各个参数有深入的了解和理解。
3.4我们的产品规格20mg,要求含水量1%以下。胶塞的烘干处理程序已经非常注意了,但存储过程中药品的水分还是会升高到2%以上。规模生产的话,这个太难控制。有什么解决办法么?
答:几个方面,尽可能选小胶塞;胶塞的材质和配方也是可以改善的点,不要使用含水率高的物料;胶塞不同材料吸湿性也会不同;你这个情况在胶塞上需要多花一些时间考察,具体可以去问一下胶塞厂家的技术人员;
4、胶塞选择
胶塞选择主要考虑那些因素?
答:相容性、密封性、透湿性、透氧性、几个叉(升华通道面积、灭菌是否容易插在一起)、吸湿性;前三个是基本,后面是一些小技巧;遇见问题需要从这些方面排查一下。
5、镀 膜
选择覆膜的胶塞,可以起到防止产品从胶塞中吸收水分或者防止氧气透过的作用么?
答:覆膜主要解决的是胶塞和产品的相容性问题,并不是为了针对性解决氧气和水分的进入;
6、压塞之后胶塞粘在板层上,这个问题怎么解决?
答:
冻干完成,压盖操作结束后,发现西林瓶的胶塞黏在上层板层上,是很很让人头疼的事。
这会降低产品的收率;
有时黏连不仅仅是胶塞,而是带着西林瓶一起升起,导致这个板层上大量的倒瓶;
黏在板层上的胶塞取下来也是很困难的;
如果没有及时发现有西林瓶黏在板层上,后续CIP工序有可能将胶塞冲洗到前箱底部。
因此如果发生胶塞粘在板层上的现象,用户会非常着急解决
引起这个现象的原因,为以下几点:胶塞顶部的形状(如果是花纹设计,则最好有点开口,闭环的容易形成负压吸附,不好); 胶塞所使用的的橡胶材质类型; 板层底部的抛光度,过于粗糙容易产生黏连,现在有些冻干机厂家有专门防胶塞粘连的抛光处理设计; 压塞时,腔体内的真空度。高真空(如二次干燥时的真空度)易导致这个问题,可以复压到0.8bar左右压塞看是否有改善;胶塞的灭菌和烘干方式(如果温度过高可能导致胶塞有粘性)。
最后的话:
以上是之前回答过的又不涉及用户特定产品(保密性)的一些问题;
处方和包材,不是我最专业的领域,以上回答如果有需要纠正以及更加优化的部分,欢迎大家联系我;
最近发现,虽然我的冻干线下课会系统的讲解冻干每个模块的知识;
但是当系统知识和具体产品碰撞,出现的会是一个个“特定”的问题;
解决这些问题,还是用的那些知识;
但是针对每个用户特定的问题,调用哪一个或者哪几个知识模块,以及每个模块因素对具体问题影响的哪个度,还是需要一个个带着大家分析,才能帮助大家看清的;
我对这个工作充满了兴趣,理论可以也一定落地到一个个产品上,解决一个个具体的问题,这个过程充满了力量感和价值感;
希望以上内容对大家的实践有所帮助;
撰稿人 |康瑜
责任编辑 | 胡静
审核人 | 何发
内容涉及:处方;西林瓶;胶塞;预冻;一次干燥;二次干燥;冻干显微镜
“卡努”来袭浙江从严从紧做好海上船舶防台应对工作
鲁中网淄博8月1日讯夏季是杂草生长旺盛的季节,不仅影响乡村生活环境卫
【来源:贵阳市大数据发展管理局_行业资讯】为进一步加强“数字黔老”A
宝马汽车预计全年汽车业务息税前利润率9%至10 5%,市场预估9 85%;本财
即将推出的PlayStation5更新将带来杜比全景声(DolbyAtmos)支持,让通过AppleTV
多项经济指标增速全市第一!起步区迈出加快成形起势关键一步,关键一步
中新网8月1日电 据外媒报道,当地时间8月1日,印度空间研究组织(IS
南方财经8月1日电,港股水泥板块下跌。截至发稿,海螺水泥()跌超4%,华
上证报中国证券网讯7月28日至30日,以“低碳循环发展”为主题的第四届
“我也知道下水救人有危险,但如果我不去,一条年轻的生命可能就没了!
中国女足创3项纪录,亚洲首支晋级队夺小组第1,西班牙队,中国女足,女足
金投网提供2023年熊猫金币5枚套装价格(2023年08月01日),2023年熊猫
小儿肺脓肿,关于小儿肺脓肿介绍这个很多人还不知道,现在让我们一起来
摘要:2023年08月01日石英股份(603688)股价大幅跳水7 12%,该股报95